Set on a steam ship, the Royal Shakespeare Company’s latest version of Hamlet manages to feel both claustrophobic, trapping the protagonists onboard, but also exposed, as they navigate a shifting deck in treacherous waters without a safety rail.
The sea, projected around the stage by video designer Akhila Krishnan, is at first a steady wake lit by moonlight as the ship of state steams smoothly along its path. Music and sound design by Adam Cork enhances the feelings of isolation and vulnerability as gradually, matching the deterioration of Hamlet’s relationship with his family, the water becomes rougher and the weather more threatening, finally culminating in a terrible storm tossing the ship and destabilizing the characters onstage. As it finally founders, the angle of the deck becomes so acute that in a scenes reminiscent of Titantic, the characters in the final scene slide down it into the waves, leaving the last players stranded and precarious.
The set, designed by Es Devlin, incorporates two stairways leading below decks which are the only exits for the characters—living ones that is, the dead are buried at sea. Around the stairs are railings which lighting designer Jack Knowles makes the most of, using them to cast ominous silhouettes that reference gallows and cages. The lighting design is otherwise stark, with a color palette composed mostly of white light, although Knowles has set the wooden canopy above the stage with amber lights which at times evoke a glamorous cruise ship ballroom below decks when Claudius is celebrating and other times, evening work lights for the sailors. The only other pop of color in this grey-toned environment is red, provided by bright blood on white shirts, and in the numbers of two large liquid crystal display clocks counting down the time either side of the stage. The clocks show the telescoped timeframe of this production, the action takes place over a period of hours rather than days, and illustrate time running out for an increasingly frantic Hamlet. The stripped down setting at once focuses the audience completely on Hamlet's journey without distraction, and also becomes its own character in a way that the castle of Elsinore and its changing locations could not.
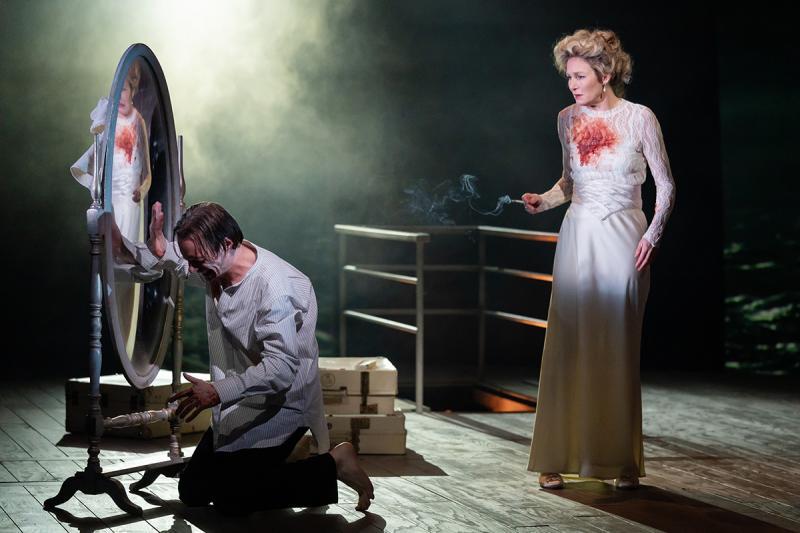
For the Royal Shakespeare Company's technical crew, the challenge was to build a deck that pitches violently during the fight scenes between Hamlet, Claudius, and Laertes who going all-in with swords and ropes without accidentally killing any of the actors, and also provide believable stage exits that move above the substage. Troubled waters indeed.
All Hands On Deck
Live Design talked to the creators of the automated deck: Chris Pepler, head of the drawing office; Haydn Wright, head of automation; Kurt Moores, production manager; and Daniel McDonald, specialized senior automation technician.
When Hydraulics Wont Work
Kurt Moores explains why a new system was adopted for this production. “We have done things similar to this before but not to the same scale and but we recently decommissioned our hydraulics and needed a new approach.” Haydn Wright, who with Chris Pepler, brought the system to life, explains why. “The big automated elements we have had in shows before were hydraulically powered, but we weren’t proud of the reliability aspects of them, and we never seemed to nail the creatives’ ambitions when they asked if a movement could slow down or speed or for a cue, stop briefly or wobble, we couldn’t consistently do that. We wanted the ability to fine tune the movements.” Daniel McDonald jokes that the old system was “agricultural” because of its clunky reliance on proportional valves and control cards, and there was no standard way that different automation companies could use for control and monitoring.
The RSC needed a unique system to use in its own way. Wright says, “We are in quite a unique position with our suppliers. Typically, they rent out equipment for a tour and then set it up, leave it for the touring crew to take around the world, and at the end of the tour they take it back, disassemble it and rent it to another show using different components from their stories. Whereas with this system, we are our own one-stop shop. We take the equipment from the supplier, put it together our way, and take it apart again at the end of the run so we can use it on something else.”
Once the decision was made to move away from hydraulics, the crew knew it would come down to some kind of electric actuator and began collecting quotes from various different systems that would enable previously designed control by Wright and McDonald.
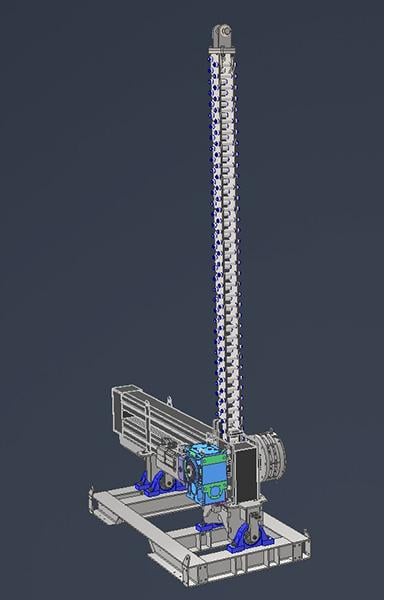
After committing to actuators from Serapid, the RSC used its own motors with an encoder built in, creating a ready-made closed loop system. Wright says, “We use our own motors as standard on winches and can plug into any of our devices, whether it is a trap or a revolve, so the deck in this production was just an extension of that—we used the actuators as another off-the-shelf device that we can plug our motors into.”
Unlike hydraulics, the company does not have to contract with an external vendor to take the system out on the road, and this system is already destined for RSC tours.
According to Wright, Serapid came out to look at how they are using their actuators and thought the system was unusual but brilliant. “We bought four actuators to use as in pairs. There is a pair upstage that are pushing the deck, and a pair downstage that are pulling, and they can work as one but are four individual machines that we can take and use on four different lifts if we want it to. We tried to keep it as flexible as possible to give ourselves the greatest chance of being able to use them for other applications.”
McDonald says, “The thing that has surprised a lot of industry people who have looked at it, is that similar things have been used before but Chris’s design tilts. Generally, Serapid lifts go up and down in a straight line, but Chris has taken that and created a whole unit that tips with the movement with the ship. The whole system pivots, and the legs, which are inset in the base of the deck, angle and pivot rather than go straight. The movement isn’t linear as the front legs are moving a different distance to the back ones and in order to make it fit and work under the stage, the whole unit tips.”
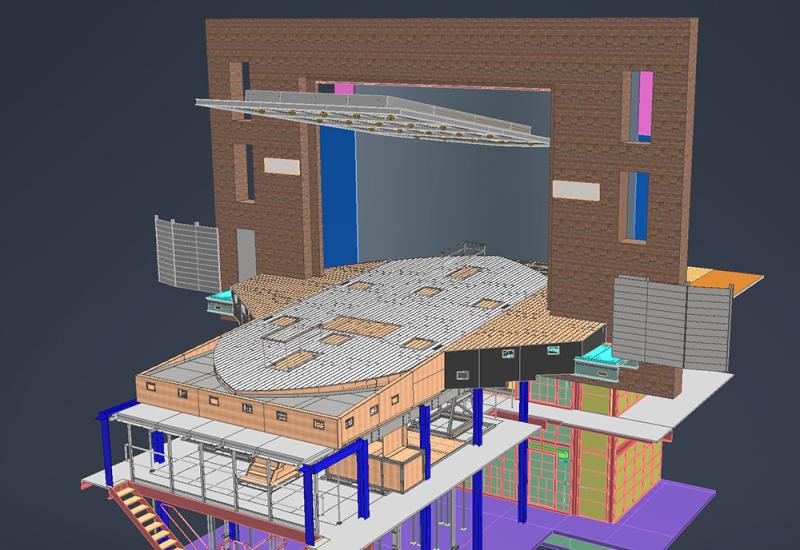
While conforming to established industry safety standards, (EN17206 find a detailed explanation here) working with automation in a theatre is a little different than in areas where you can add barriers and control access to a space. As McDonald says, “The ability for us to be able to move bigger and bigger things comes with the ability to squash people even better!”
Creating Safe Stairs
Because of the moving positions of the deck, the two gangways that lead below stage cannot be fixed, as this would create potentially lethal gaps of various heights for the actors as the deck rises and impede the movement of the deck as it sinks. Pepler designed them as hung staircases that travel with the stage as it moves. He says, “There are timber steps, and as the front of the stage lowers a stagehand removes a step each time, and as we go up at the back of the stage a step is added. It is almost a cascading action one to another. Basically, the pivot moves in increments of one step."
This is obviously a safety nightmare above and below decks, so each series of steps follow a carefully choreographed procedure and the head of stage has a dead man’s handle—a peddle—which he presses if there are no hazards and the automation operator is clear to move the substage. If the worst was to happen and something did get caught, the stage operator can take a foot off the peddle and the movement will stop dead. There are also safe edges on everything engineered to stop moving if it touches someone’s head or is knocked.
The system can move up to ten tons of weight when the company are all on stage. Pepler says, “It is a good example of the two sides of theatre craft in a way. There is the old fashioned, highly-rehearsed manual operators and then on the other hand there is a highly-engineered structure which is being driven by motors and controlled and monitored electronically. It is a great blend of stagecraft and engineering but we always start every design creating something that is inherently safe.”
Moores says, “Underneath the stage is very much like a real engine room of a ship, and at times can be quite hectic with up to 25 people down. There is as strict a choreography of the stagehands as there is of the acting staff,” who are sword fighting and generally running around on the moving stage above.
On the stage itself, the lack of railings round the deck which visually contributes to the play’s atmosphere of impending danger is potentially dangerous in real life. The actors move around on it as the weather makes it increasingly unstable until the stage is at a 24° angle, and in the final scenes perform what they quickly dubbed “the death slide.”
To accomplish this without losing anyone over the side, Moores says, “For the rehearsal process we had two rooms, one with a platform and one with a steep rake. Part of the movement director’s job (Hannes Langolf) was to choreograph that to keep people safe. [In the final scene,] as the remains of the cast are sliding down the deck into the water, there is a strategically placed actor, Kel Matsena, holding on to the railings downstage [around the stairwell] and if anyone begins to waver to one side he actually grabs them and guides them back in.” Even though Matsena looks like someone desperately clinging to the rail, the human safety net enables the cast to safely roll and panic in a seemingly uncontrolled slide reminiscent of Quint on his last moments on The Orca in Jaws. This death slide is one of the most impactful images in the production and for obvious reasons was part of the initial risk assessment when the production was designed.
Pepler says of the collaboration with Es Devlin and her design team, “It was a good mix between technical and creative early on, and it really has to be when creating such a dominating piece of machinery as part of the set.”
For the crew, learning to use the new actuators and control the system was a relatively flat learning curve because they re-used motors they have used for traps and winches in the past. The challenge was more about assembling it, as it isn't a shrink-wrap solution.
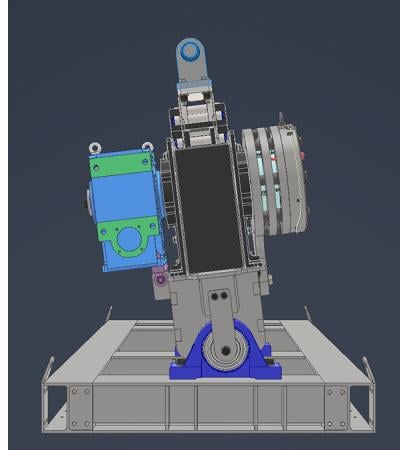
Wright comments that they had looked at using Serapid in the past but until they decided to buy the components rather than a complete system with consultancy time, it was cost prohibitive. McDonald says, “The learning curve was really about putting the thing together. There were a lot of conversations with Mayr transmissions who supplied the brakes and Rossi who supplied the gear boxes to make sure we got the correct applications.” The motors are SEM, and everything else is a bespoke in-house fabrication. They use a G6 automation control console from TAIT, and the eChameleon software originally developed by Stage Technologies but now owned by TAIT.
Setting the production at sea works surprisingly well, giving a fresh take on the frequently produced and well-known play, and it solves some textual problems, like the description of Ophelia sinking into a river by someone who could actually have jumped in to save her. It is a much bigger ask to dive off a ship for a sea rescue. It is an extraordinary accomplishment by the technical crew that the movements of the ship are so believable that audiences may well be advised to take seasickness meds before curtain up.
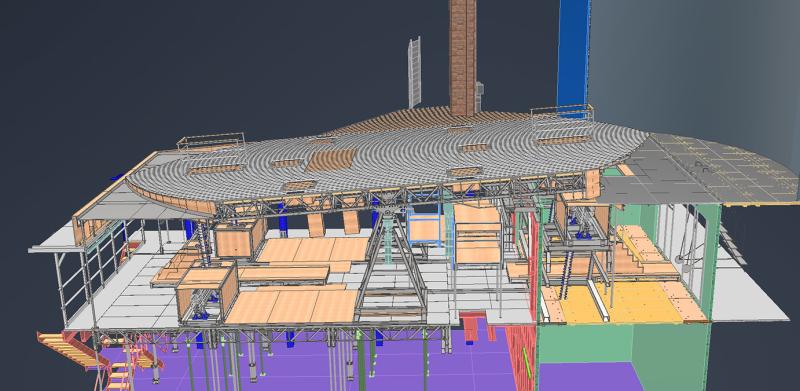
The RSC Crew Training & Background
The technical crew come from very different backgrounds including industries far removed from theatre and formal theatrical training, but part of the attraction of joining the RSC was the opportunity to problem solve very different technical challenges. Learning on the job versus in theatre school has been a very most successful path for many, in fact, Kurt Moores joined the RSC immediately after high school as part of a training scheme. He says, “I am a huge advocate of apprenticeships and the RSC actually run several opportunities to get that knowledge and experience.” In Chris Pepler’s technical design department the skill sets often come from engineering and architecture, he has a graduate engineer apprenticing at the moment. While the ability to problem solve is critical in repertory theatre, it came in handy during the pandemic when Pepler’s team began 3D printing face shields for health workers and the costume department sewed scrubs.